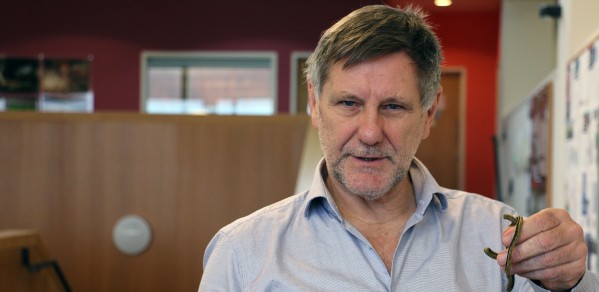
An interview with Professor Steve Evans, Director of Research at the Centre for Industrial Sustainability, part of Cambridge University's Institute for Manufacturing.
If manufacturers moved just half way from their current resource usage towards the usage of the most efficient companies in their own industry, our research indicates that the impact in manufacturing would be 12% increased profit, 15% more jobs and 5% reduction in greenhouse gas emissions.
Professor Steve Evans
"By the end of this talk, I want you to feel really angry."
Not your conventional opening line to a talk but then it's not every day a speaker brings along a bag of sock tops to pass around.
By the time Professor Steve Evans gathers them up again, some have been twisted and knotted into intricate shapes. Members of the audience have started to make things.
And that's the point. It's not hard to imagine these colourful, stretchy scraps turned into anything from blankets to bags to belts. And yet, every year, says Evans, 11 billion of these fabric edges are cut off during machining and discarded as waste.
"Sock tops are a great example of the 'invisibility' of some forms of waste to those who see it every day. Manufacturers don't always notice the little bits cut off. They notice the pile of socks – a pile of money – being made. It's easier to follow the money than to notice the waste."
"I study the shadow," he adds. "I look not at what's manufactured but what has been lost or not used during the process. Around 90% of the resources we process to create goods are not reaching the person for whom they are made, 50% of edible food is not eaten, and only about 50% full loading is achieved in freight trucks in the UK.
"These are examples of what makes me angry."
Sock tops
Professor Steve Evans is Director of Research at the Centre for Industrial Sustainability, part of Cambridge University's Institute for Manufacturing. Over the past 20 years, he and his team of action researchers have been chasing down the 'shadows' of wasteful inefficiencies cast by the manufacturers of anything from cement to cars to clothing.
"There are examples of inefficiency and waste all around us. But it's either 'part of the furniture' of operations or you can't see it – it's the water used or the energy consumed," he says.
"Factories are responsible for about 36% of greenhouse gas emissions globally, and often the carbon footprint of manufacturing operations is closely related to how efficiently they operate. It's crucial for profit margins that resource efficiency is the best it can be and it's crucial for the planet that industries reduce their carbon footprint."
Evans points to Toyota as being a leading light in industrial sustainability. "The factory in Burnaston, near Derby, has been reducing the energy it uses to manufacture a car by at least 8% every year for 14 years, resulting in over 70% reduction over the period. They can now make four cars for the energy it used to take to manufacture one car 14 years ago.
"Then they started a programme called 'no production equals no energy'. That means when the factory is shut down in the middle of the night, they shouldn't be using energy. Crucially, they've managed to do all of these improvements by identifying efficiencies in energy usage, not by depending on a major new technology to revolutionise the business."
His team has now had what amounts to thousands of interactions with industries – including Toyota, Airbus UK, Jaguar/Land Rover and Dyson – either directly or indirectly through use of their open source tools. As a result, Evans and colleagues can spot patterns in the inefficiencies that hold industries back from performing better.
"None of us wants to solve one problem at a time, so we're always looking for patterns across multiple industries, pinpointing places where resources are wasted and where opportunities are missed for creating value.
"Quite often, we don't need to collect much more data or even any at all, but we do help them to present the data they've already collected in their own factory in different ways.
"And all of a sudden, it goes from being just numbers in the spreadsheet to them saying 'I can now see the waste!' All we're doing is asking the right questions and presenting the results in a way that makes the invisible visible."
“Sometimes it's as simple as asking what happens on your best day and what happens on your worst day, and then asking why."
Take for instance... 'what's the best day to make cement?'
"The cement industry is the second most intense industrial producer of CO2, responsible for around 5% of global emissions. If it were a country it would rank as the third highest producer of emissions after China and USA," says Evans.
It's also an industry of low margins and high capital, with many plants now decades old and inefficient. Although there has been a trend towards increasing use of alternative fuels, moving towards improved sustainability might seem too daunting a task for some businesses to take on.
Evans agrees that the perception of sustainability as being a complex add-on can be a deterrent: "Often it's easier to reach into your wallet than to reach into your brain," says Evans. "But what if you had a clear business case to show that improved sustainability would also help your bottom line? And that it could be achieved with today’s existing technologies, rather than waiting for new technology to be invented?"
In particular, given the diversity of materials being used as alternative fuels by the cement industry, the exact relationship between fuel mix, costs and CO2 emissions has not always been clear.
Dr Daniel Summerbell from the Centre for Industrial Sustainability looked at day-to-day variations in the performance of three UK cement plants to see whether existing industries could improve their efficiency through changes that don't rely on capital investment. He looked at the best day and the worst day for greenhouse gas emissions. The gap was huge.
"Most industries look at the overall performance of whatever aspect they are concerned with," explains Evans. "By asking which day was the best, we helped them see that a different metric could be used to understand how to perform better."
Improving the fuel mix reduced fuel consumption by about 6% and fuel-derived CO2 emissions by as much as 16%.
"Although such improvement is subject to availability of appropriate fuel and operating conditions, the low capital requirement makes it very attractive to industry," adds Evans.
"I like to describe the solutions we come up with as 'stop doing stupid stuff'."
When it comes to sustainability and the environment, 2019 has been a significant year, says Evans.
"Things changed in 2019. Public perception of climate change has increased. Young people are asking questions of the older generations. The other day I was contacted by a CEO to talk about sustainable industry after his teenage daughter asked him 'Dad what are you doing about climate change?' "
Where five years ago Evans and his team were mainly working with pioneering companies who saw the need for sustainable manufacturing, increasingly they are working with those who've never had sustainability on the agenda. Meanwhile they're seeing the early adopters looking to speed up their efforts.
But, for industrial sustainability to be more widely achieved, he believes it's essential that companies don’t exist in silos, where one company works out a clever trick and then says ‘job done’.
"We need to understand how to scale these solutions if we are to eliminate greenhouse gas emissions by 2050, as the world needs and as the UK government has legislated," he says. "To make efficiency improvements more achievable for manufacturers, scalable, practical and easy-to-use tools are required."
Evans and colleagues have developed the open-source Cambridge Value Mapping Tool to help companies recognise where value is being captured, and where it is not, using a structured visual approach. And they've been collaborating with Manufacture 2030, which provides a cloud-based platform to help manufacturers use less energy, water and materials, and thereby cut operational costs and environmental impact.
"What we don't do is tell people what to do in their factories – ever. Instead we think the key ingredients to solving these sustainability challenges are management support, freedom to think and education to stop doing stupid stuff. After that it's common sense."
In fact, when Evans became a Professor, he was asked what title he would like. Professor of Common Sense, he said. The appointing committee laughed. It raises a point however about how Evans sees the world of industrial sustainability.
"Nothing surprises me. In fact when I see examples of stupid stuff, I no longer have jaw-dropping moments. I just go 'Oh, there's another one'. But I'm really interested in why what we think of as normal common sense is so rare. That's why I use examples like the tops of socks. People get it straight away."
Words and photography: Louise Walsh