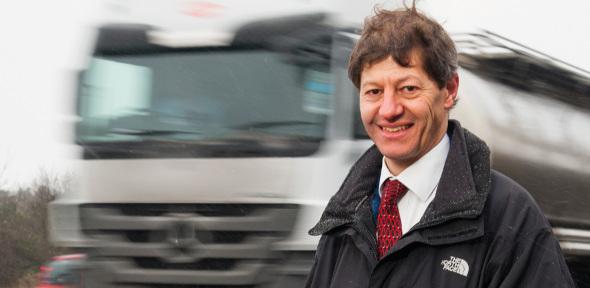
Braking technology set to shave a massive 25% off truck stopping distances looks set to come to fruition this year. However, its developers believe their systems may not be widely available for at least five years, possibly double that. That's despite the considerable and obvious benefits, in terms of preventing accidents, mitigating others, saving lives, reducing accident damage, and cutting downtime and insurance premiums.
At the moment, in an EBS stop, the wheels of an artic successively lock and unlock every second, which is extremely inefficient, cars don't suffer the problem because, although the control strategies are similar, their hydraulics are much faster. But on trucks, the EBS effectively slams the tyres from one end of the friction slip curve to the other. And every half second, when the tyres accelerate back to free rolling, the brakes generate no stopping force at all.
Professor David Cebon
So why not? Partly, developers at the Cambridge Vehicle Dynamics Consortium (CVDC) make the point that there is still a formal engineering process to be followed, and these things take time. Fine, but not a decade – particularly given the eight years' of development to date and the fact that the technology is now ready for track testing at MIRA's proving ground. No, it seems the reason for the extended timeframe stems from a belief that truck manufacturers won't stump up any additional cost, if they're not required to do so by legislation. All the more so given that their customers, the operators, are already being asked to pay the price hike of Euro 6, which comes into force in 11 short months.
Is this a realistic assessment? Well, that depends on everything from the results of a dispassionate cost-benefit analysis of the technology, to the potential for a public and/or industry outcry. As John Davies, head of UK services and support at MAN, says, as long as it's not technology for technology's sake and the new system can prove a safety case, truck manufacturers would almost certainly want it. "Everyone wants to drive the safest truck on the road, and the industry is always keen to embrace anything that adds to road safety, whether passive or active. Look at disc brakes 25 years ago and more recently EBS [electronic braking systems]. Neither were legal requirements, but all manufacturers adopted them."
There's the test. So let's backtrack to the technology and establish its real significance. Professor David Cebon, director of CVDC (which comprises engineers at Cambridge University and big truck industry names, including Haldex, Goodyear, Firestone, Volvo Trucks, AB Dynamics, Tridec, Poclain Hydraulics, Wincanton, SDC Trailers and MIRA) describes it as involving two new components – hardware and software. Each, he says, is equally important, because together they tackle the limitations of today's EBS and ABS (anti-lock brake system) systems – namely slow brake valves and long pneumatic pipelines, which delay brake response, as well as sub-optimal brake control algorithms that date back to the 1970s.
"At the moment, in an EBS stop, the wheels of an artic successively lock and unlock every second, which is extremely inefficient," he explains. "Cars don't suffer the problem because, although the control strategies are similar, their hydraulics are much faster. But on trucks, the EBS effectively slams the tyres from one end of the friction slip curve to the other. And every half second, when the tyres accelerate back to free rolling, the brakes generate no stopping force at all."
Cebon argues that, to minimise stopping distances, braking tyres must be maintained at peak stopping force, without slipping. So let's look at the detail. First, you need to know where the top of the friction curve is. That means software and sensors that can estimate tyre friction as it changes, on the move. "Our system can do that in about half a second, by measuring brake pressure and wheel speed, using conventional sensors," he says.
Secondly, the system has to know the vehicle road-speed (not the slipping wheel speed). "We get that from accelerometers and gyros that can live in the brake ECU. Our system is like an inertial navigation system but much lower cost, because we're only interested in estimating motion in the 20 seconds or so of an ABS stop."
Thirdly, radically different software is required, capable of continuously controlling brake pressure at each wheel and maintaining tyre slip at the top of that torque curve. "For that, we have developed new, non-linear control algorithms, capable of tracking the target tyre slip level, even in the unstable region past the peak of the friction curve."
And finally, you need much faster brake hardware. CVDC has achieved that with two innovations. First, the team moved the pneumatic control valve away from centre of vehicle ECU, instead locating one unit on each brake chamber. That eliminates pneumatic delays and enables fast individual wheel braking. But secondly, working with Camcon and Haldex, the team has developed a new pneumatic control valve that is 10 times faster than conventional solenoid valves.
"It's essentially an electromagnetic valve, which uses a flexure and binary actuation technology to flip back and forth to open and close the air port," explains Cebon. "It took three years to perfect but we've brought it to a level where it now reliably switches full brake pressure within 3msec, compared to solenoid valves' 40msec."
Why does it need to be so fast? Cebon gives the example of truck wheels traversing rough ground and causing the load on the tyres to change, potentially at up to 10—12Hz. "So the brake torque has to be continuously modulated at that frequency, too, to keep the tyre force correct. That's where today's brakes fall down, because they oscillate at 1Hz. Our system is much faster, so we can control wheel slip accurately under all conditions."
Hence CVDC's claim of a 25% improvement in stopping distances, compared with today's best EBS. And hence also its suggestion of secondary weight, cost and energy savings. "Our system reduces air consumption by about 50%, because instead of filling and dumping the brake chambers every second, it quickly slides up to the desired brake pressure and stays there, rapidly modulating around that point. So manufacturers will be able to use smaller air tanks and compressors," insists Cebon.
So there you have it. Six of the new brake valves have been built and are currently being installed on a three-axle semi-trailer, which is now being prepared for testing with the new control system at MIRA next month. Phase two will see the technology installed on a tractor unit, later this year or early in 2014.
"We will prove the technology outside the lab and in real road conditions this year. Widespread uptake will then depend on the industry," comments Cebon. And he makes the point that adoption need not be restricted to new vehicles alone. "The system could be be retrofittable and compatible with all other braking developments, including the new AEBS [advanced emergency braking systems]."
This article is reproduced with the kind permmission of the Transport Engineer magazine where it originally appeared in February 2013: www.transportengineer.org.uk/article/47640/Braking-revolution-.aspx