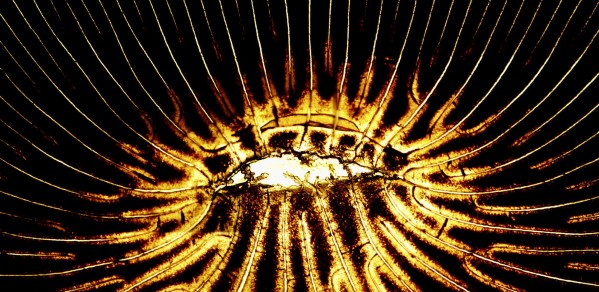
Dr Ronan Daly, from the Institute for Manufacturing's Inkjet Research Centre and founder of the new Fluids in Advanced Manufacturing Group, explains why taking a cross-disciplinary approach to manufacturing research has the potential to deliver solutions to some of the world’s most pressing problems.
We aim to use insights from our research to develop groundbreaking, simple, robust and affordable solutions that can be made at a commercial scale.
Dr Ronan Daly
Advances are being made all the time in our understanding of – and ability to create and manipulate – biological and synthetic building blocks and nanoscale materials. Research in these areas has the potential to help us tackle a host of important global challenges: reducing the amount of energy we use, removing pollutants from our environment, identifying diseases more rapidly and inexpensively and even delivering medication personalised to each patient.
However, while these new materials hold much promise they are often extremely fragile or sensitive to their environment. If they are to be developed for commercial use, we need new manufacturing technologies that can integrate these very delicate components into functional materials, sensors and bio-diagnostic devices.
Last year we set up the Fluids in Advanced Manufacturing (FIAM) group at the Institute for Manufacturing (IfM) to do something genuinely new. It brings together fundamental laboratory research in a range of disciplines – chemistry, nanoscience, fluid mechanics and interfacial science – with research into manufacturing techniques and processes. It is because we understand the sensitivity of the components at the molecular scale during processing that we are so well placed to develop new and effective fabrication techniques.
We aim to use insights from our research to develop groundbreaking, simple, robust and affordable solutions that can be made at a commercial scale. The IfM provides a unique environment in which to do this, with science and technology researchers – many of them with industrial experience – working alongside experts in management and policy. So our research is grounded in a broader manufacturing context which takes account of things like the technology management challenges associated with research and development (R&D) and the supply chain, service and sustainability issues underpinning the commercialisation of new technologies as well as the implications of national and international policy developments. The IfM approach is also predicated on collaboration with industry. This is particularly important for FIAM, where close links with industry are necessary, both to further the research and to understand the particular challenges of manufacturing scale-up.
Our research is centred around four themes, the first of which is concerned with the creation and manipulation of soft matter while the second focuses on manufacturing technologies that can shape these new materials into active elements such as sensors. The third theme looks at novel ways of integrating these materials into 3D microscale architectures to create new devices. We do all of this within the context of the fourth theme: understanding the broader challenges of transforming laboratory research into an appropriately scaled-up proposition.
Soft-matter manufacturing research
We control, manipulate and structure polymers, gels and biological materials in order to develop highly versatile materials with a vast array of different chemical, physical and biological properties. The challenge is that they all need to be processed carefully because they are highly susceptible to damage or alteration during manufacturing. Stresses during flows or temperature gradients can change the chemical structure completely and lead to unpredictable behaviour. To counter this, we are combining top-down patterning techniques with molecular scale and microscale self-assembly to control the positioning and structure of these materials, while still maintaining their molecular function.
One of the areas we are most interested in is tissue engineering applications and drug delivery devices. To create better in vitro techniques for testing new drugs and also to improve cell, tissue and organ replacement therapies, we want to replicate the natural conditions for cell growth and tissue formation. FIAM doctoral student, Qingxin Zhang, is looking at how liquid engineering can be used to build polymer microstructures containing materials such as small-molecule drugs. To tackle the manufacturing challenge, she is combining a self-assembly technique with a controllable digital patterning of liquid drops (by inkjet printing) on to liquid surfaces. These are then guided to selforganise into patterns that will eventually support cell growth and the slow release of drugs.
We are also working with the School of Chemistry in Trinity College Dublin to look at complex self-assembled systems at the molecular scale and their integration into manufacturing. Other projects in the pipeline include the development of reactive inks for 3D manufacturing and inkjet printing of pharmaceuticals into usable devices.
New digital manufacturing techniques
Responding to insights emerging from the UK Government’s 2013 Foresight report on the Future of Manufacturing, we are particularly interested in low-volume, flexible manufacturing techniques. These techniques help manufacturers switch rapidly between different product variants or change to entirely new lines through simple reprogramming. They will support the development of a new generation of business models based on product personalisation.
Our research focuses on using digital fabrication techniques to enable novel platform technologies that can be used in environmental sensing, biosensing, drug delivery and biomaterial design. These techniques need to be compatible with a new range of materials and must be able to integrate biological components (antibodies and proteins, for example) as well as advanced functional materials, such as nanowires, carbon nanotubes and a range of 2D materials.
FIAM’s Yoanna Shams is researching a hybrid technology which combines additive techniques such as advanced lithography with subtractive techniques, using ultra precision lasers to remove and shape the materials. This combined approach allows us to overcome some of the challenges that inkjet techniques still face and to manufacture sensors from a wide range of advanced functional materials. The project brings together support from the Engineering and Physical Sciences Research Council (EPSRC) Centre for Doctoral Training in Ultra Precision, industrial partner M-Solv Ltd and the Centre for Science, Technology and Innovation Policy (CSTI) to put into practice our approach of ensuring laboratory research has a path to real application.
Device fabrication
Later this year we will be starting a project on the fabrication of point-of-care diagnostics, in collaboration with Professor Lisa Hall from the University of Cambridge's Department of Chemical Engineering and Biotechnology. This is a rapidly growing area within the medical technology sector where low-volume, personalised manufacturing has the potential to revolutionise healthcare. In this context, we are particularly interested in paper as a substrate material. It has the great advantage of being an inexpensive, sustainable material and we already know a lot about its absorbance, chemical and optical properties. We want to use it to absorb a sample which then reacts with a sensing element to generate a diagnostic result. The downside of paper is the random nature of both its structure and chemistry: our research aims to integrate the biological and sensing components into it in such a way that the device remains both sensitive and robust.
Pathways to manufacturing
Our fourth theme is as much about the research culture of the group as it is a distinct area of research. The theme, developed in collaboration with CSTI, examines the broader challenges of translating emerging technologies from laboratory research to a commercial scale.
The ‘scale-up journey’ needs to take account of a range of manufacturing challenges, such as production technologies, system integration, downstream supply chain effects, sustainability, regulatory demands and so on. Working with CSTI colleagues, we are developing a systematic approach to identifying and addressing risk factors early on in order to maximise the chances of successful commercialisation.
The future
We are passionate about each of these four areas of research and success in any one of them will result in significant economic and social benefits. By bringing them together in such a way as to understand the scientific, manufacturing and business and policy challenges, we are in a position to do something really exciting. Advanced manufacturing research needs to be able to bridge these disciplines and we are building a team of people and partner companies determined to create breakthrough opportunities for emerging technology enterprises.
After graduating from the University of Edinburgh with an MEng in Chemical Engineering with European Studies, Ronan became a Process Technology Manager for Unilever R&D, working with global brand teams to tackle formulation, scale-up and supply chain innovation challenges. His PhD from the School of Chemistry and the Centre for Research in Adaptive Nanostructures and Nanodevices (CRANN), Trinity College Dublin, led to a new-found passion for novel manufacturing techniques. In 2011 he joined the IfM’s Inkjet Research Centre to continue his work on biosensor platforms using digital fabrication techniques and inexpensive materials for commercially targeted tests.
FIAM is looking for industrial partners. If you would like to find out more, contact Dr Ronan Daly (contact details top of page, right hand side)
This article originally appeared in IFM Review.