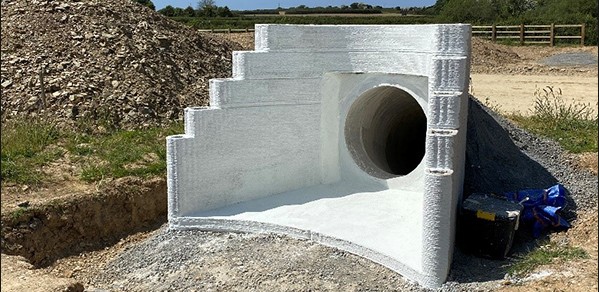
Cambridge researchers, working in partnership with industry, have helped develop the first 3D printed piece of concrete infrastructure to be used on a National Highways project.
Making the wall digital means it can speak for itself, and we can use the sensors to better understand these 3D printed structures and accelerate their acceptance in industry.
Professor Abir Al-Tabbaa
The 3D printed structure – a type of retaining wall known as a headwall – has been installed on the A30 in Cornwall, where it is providing real-time information thanks to Cambridge-designed sensors embedded in its structure. The sensors provide up-to-date measurements including temperature, strain and pressure. This ‘digital twin’ of the wall could help spot and correct faults before they occur.
Headwall structures are normally made in limited shapes from precast concrete, requiring formwork and extensive steel reinforcement. But by using 3D printing, the team – including specialists from Costain, Jacobs and Versarien – could design and construct a curved hollow wall with no formwork and no steel reinforcement. The wall gets its strength not from steel, but from geometry instead.
The wall – which took one hour to print – is roughly two metres high and three and a half metres across. It was printed in Gloucestershire at the headquarters of the advanced materials company Versarien, using a robot arm-based concrete printer. Making the wall using 3D printing significantly saves on costs, materials and carbon emissions.
Over the past six years, Professor Abir Al-Tabbaa’s team in the Department of Engineering has been developing new sensor technologies and exploring the effectiveness of existing commercial sensors to get better-quality information out of infrastructure. Her team has also developed various ‘smart’ self-healing concretes. For this project, they supplied sensors to measure temperature during the printing process.
Temperature variations at different layers of the 3D printed wall were continuously monitored to detect any potential hotspots, thermal gradients, or anomalies. The temperature data will be correlated with the corresponding thermal imaging profile to understand the thermal behaviour of the 3D printed wall.
“Since you need an extremely fast-setting cement for 3D printing, it also generates an enormous amount of heat,” said Professor Al-Tabbaa. “We embedded our sensors in the wall to measure temperature during construction, and now we’re getting data from them while the wall is on site.”
In addition to temperature, the sensors measure relative humidity, pressure, strain, electrical resistivity, and electrochemical potential. The measurements provide valuable insights into the reliability, robustness, accuracy, and longevity of the sensors.
A LiDAR (light detection and ranging) system also was used to scan the wall as it was being printed to create a 3D point cloud and generate a digital twin of the wall.
“Making the wall digital means it can speak for itself,” said Professor Al-Tabbaa. “And we can use the sensors to better understand these 3D printed structures and accelerate their acceptance in industry.”
The Cambridge team developed a type of sensor, known as a PZT (Piezoceramic Lead-Zirconate-Titanate) sensor, which measures electromechanical impedance response and monitors changes in these measurements over time to detect any possible damage. These smart sensors can show how 3D printed mortar hardens over time, while simultaneously monitoring the host structure’s health.
Eight PZT sensors were embedded within the wall layers at different positions during the 3D printing process to capture the presence of loading and strain, both during the construction process and service life after field installation.
The team, which included experts in smart materials, automation and robotics and data science, also developed a bespoke wireless data-acquisition system. This enabled the collection of the multifrequency electromechanical response data of the embedded sensors remotely from Cambridge.
“This project will serve as a living laboratory, generating valuable data over its lifespan,” said Professor Al-Tabbaa. “The sensor data and ‘digital twin’ will help infrastructure professionals better understand how 3D printing can be used and tailored to print larger and more complex cement-based materials for the strategic road network.”
Members of the team included Dr Sripriya Rengaraju, Dr Christos Vlachakis, Dr Yen-Fang Su, Dr Damian Palin, Dr Hussam Taha, Dr Richard Anvo and Dr Lilia Potseluyko from Cambridge; as well as Costain’s Head of Materials Bhavika Ramrakhyani, a part-time PhD student in the Department of Engineering, and Ben Harries, Architectural Innovation Lead at Versarien, who is also starting a part-time PhD in the Department of Engineering in October.
The Cambridge team’s work is part of the Resilient Materials for Life (RM4L) Programme and the Digital Roads of the Future Initiative, which are supported in part by the Engineering and Physical Sciences Research Council (EPSRC), part of UK Research and Innovation (UKRI), and the European Union.
Written by Sarah Collins. This article first appeared on the University of Cambridge website.
About the headwall and its location
The A30 (Chiverton to Carland Cross Scheme) is a road of strategic importance, having been identified as part of the UK Government’s Roads Investment Strategy, with an £8 million contribution from the European Regional Development Fund already committed.
The completed headwall at this site stands testament to months of collaborative work and preparations involving a team from Costain, Versarien and the University of Cambridge – a team who took this idea from the concept stage to design and construction and finished with on-site installation.
A rapid-setting alkali activated mortar mix was deployed, which was slightly adjusted by tuning the retarder admixture dosage levels as the height of the wall increased, enabling the full construction of the wall, weighing 2.3 tonnes and measuring 2.7m x 1.9m and 1.8m high, to be completed in around one hour.
In the 3D printed headwall construction process, temperature monitoring plays a crucial role due to the use of a rapid setting cementitious mix and the generation of heat during the reaction. To manage thermal stresses and prevent durability issues like crack formation, the wall was continuously cooled down by water jets.
University of Cambridge expertise
The contribution from the Cambridge team was in the deployment of several innovative embedded and surface sensors to aid in understanding the performance of the wall during its construction and afterwards on-site, throughout its service life, under real mechanical and environmental stresses.
Over the past six years, Professor Al-Tabbaa’s team have been developing novel in-house sensor technologies and exploring the effectiveness of a range of commercial sensors as part of the EPSRC-funded Resilient Materials for Life (RM4L) programme grant.
RM4L developed a range of biomimetic cementitious materials and structures to include the following attributes: self-healing, self-sensing, self-immunising and self-reporting.
This work culminated in the team deploying those sensors as part of the fabrication of large concrete beams that contained a range of the developed biomimetic materials and products. These were then subjected to a range of aggressive environments and damage scenarios.
The sensors were used to capture the effect of the biomimetic materials on the production process, compared to control beams, and their performance in response to damage thereafter. The sensors measured temperature, relative humidity, pressure, strain, electrical resistivity and electrochemical potential. The measurements have been on-going for almost a year, providing valuable insights into the reliability, robustness, accuracy and longevity of the sensors, as well enabling the development of correlations between the various measurements.
A sub-set of those sensors was taken forward for field-scale deployments within the 3D printed headwall. In addition, a LIDAR system was used to scan the headwall as it was being printed to create a 3D point cloud and generate a digital twin of the wall.
The Maturix temperature sensors (Type K Thermocouple and Gaia 200 transmitter) were installed at different layers of the 3D printed wall. They were programmed to collect data every 15 minutes and can wirelessly transmit the collected data to the cloud using Sigfox antennas or gateways.
Sigfox is a wireless communication protocol designed for low-power, wide-area networks (LPWAN), which enables the sensors to send data over long distances with low energy consumption, making them well-suited for applications where sensors need to operate for extended periods without frequent battery replacements or recharging. Once in the cloud, the temperature data can be continuously monitored through a dedicated portal. This portal serves as a centralised platform for data visualisation, analysis and reporting.
By mapping the temperature profile spatially and temporally, the team monitored the maturity, strength, and microstructural developments of the mortar in real-time during the construction phase. Temperature variations at different layers of the 3D printed wall are continuously monitored to detect any potential hotspots, thermal gradients, or anomalies. The temperature data was then correlated with the corresponding thermal imaging profile to understand the thermal behaviour of the 3D printed wall.
PZT sensors, developed in-house as part of RM4L and successfully tested as part of the large concrete beams, were also deployed here. Through utilising both the direct and the inverse properties of these smart PZT sensors, the sensors were able to provide valuable insights into the hardening of the 3D printed mortar over time, while simultaneously monitoring the hosting structure’s health condition. To enhance the sensors' sensitivity and insulation properties, the sensors were coated with epoxy resin. This minimises the randomness in the interfacial zone between the PZT sensors and the hosting 3D printed structure, therefore increasing the repeatability and reliability of the sensor readings.
Eight PZT sensors with a 15mm diameter and 2.1mm thickness were embedded within the headwall layers at different positions during the 3D printing process. This was done to provide sufficient spatial distribution of data across the entire structure to capture the presence of loading and strain, both during the construction process and service life after field installation. With a relatively high curing temperature, of 320°C, these types of PZT sensors show a stable response when exposed to different ambient temperatures.
In collaboration with Utterberry, the start-up by Cambridge alumna Dr Heba Bevan, several Utterberry displacement, tilt, and temperature sensors were also surface mounted at various locations on the headwall to fully monitor structural integrity during construction and when in service. The sensors can detect minute tilt and displacement within the entire 3D printed structure, allowing remote monitoring of the wall in the site conditions. The system is also capable of detecting leaks within the layers to send alerts if it is breached in any way. The sensors onboard artificial intelligence and machine learning allow the sensors to communicate and give predictive warnings to preserve the integrity of the structure.
Leveraging the interdisciplinary expertise within the research team, which spans smart materials, automation and robotics and data science, the team was able to develop a novel bespoke wireless data-acquisition system, which enabled the collection of the multifrequency electromechanical response data of the embedded PZT sensors remotely from Cambridge. The wireless system was designed to actuate the PZT sensors within their planner vibrational mode, hence acquiring the hosting structure’s localised dynamic response through the monitoring period. The data from the PZT sensors are being correlated with the Maturix and Utterberry sensors.
The researchers also employed LiDAR technology to scan the headwall as it was being printed. LiDAR utilises laser pulses to create 3D point clouds of objects and environments. The LiDAR scans were collected using stationary and non-stationary systems. The stationary LiDAR data was collected using a FARO Focus 3D scanner, consisting of a laser unit mounted on a tripod positioned ~5m from the head wall. The non-stationary scans were collected with a handheld Kaarta Stencil 2 scanner, which was operated at ~5m around the headwall. The data from both scans will be combined to create a 3D point cloud of the headwall over time, allowing any geometrical changes during the print to be captured. The point cloud data will be converted into a 3D mesh, which will serve as the foundation for generating a digital twin or virtual replica of the head wall. Data from the various sensors will then be integrated into the digital twin, enabling the simulation of the physical headwall’s behaviour and performance and digital twin forensics and forecasting.
The instrumentation and generation of a digital twin of the UK's first 3D printed headwall for the strategic road network is a groundbreaking achievement that marks the beginning of a new era in infrastructure development. This project will serve as a living laboratory, generating valuable data throughout its lifespan. Furthermore, the sensors data and ‘digital twin’ will help infrastructure professionals better understand the 3D printing of cementitious materials and how they can be used and tailored to print more complex and larger objects on the strategic road network. This project will play a crucial role in shaping the development of future infrastructure projects and marks a step change in the way we construct and maintain our road network and other civil engineering structures.
The Cambridge team's efforts as part of the Digital Roads of the Future Initiative are at the forefront of this exciting enterprise and are paving the way for a safer, more efficient, and more sustainable infrastructure.