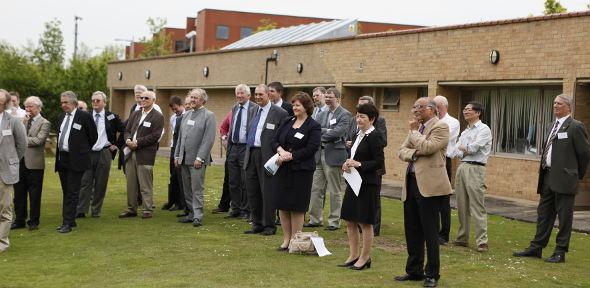
The Vice-Chancellor, Professor Alison Richard, started the University's first wind turbine at a ceremony at the West Cambridge site. The new 20kW wind turbine is fitted with a revolutionary generator, known as the Brushless Doubly-Fed Induction Generator (BDFIG), which has been the subject of research at Cambridge over the past 10 years.
Designed by Dr Richard McMahon and his team at the Department of Engineering in collaboration with Durham University and Wind Technologies, a Cambridge University spinout, the BDFIG considerably improves upon the reliability of existing generators, which is an essential requirement for the next generation of offshore turbines. Dr Richard McMahon gave an excellent speech at the ceremony which is given in full below.
Following the successful completion of the 20kW project, researchers are currently building a medium-scale 250kW BDFIG, as a stepping stone to a multi-megawatt machine, which will be built and tested next year.
Speeches at the ceremony were given by Professor Dame Ann Dowling, Head of the Department of Engineering, Professor Gehan Amaratunga, Head of the Electronics, Power and Energy Conversion Group, and Dr Richard McMahon, Head of the Renewable Energy Group. Below is Richard's speech.
How we got here
About 100 years ago it became clear that electrical power would be generated and distributed as AC for compelling technical reasons. The generation side was straightforward, the preferred electrical machines were the synchronous generator, or alternator, conveniently operated at fixed speed.
However, electrical drives were a problem. Tesla's induction motor had no connections between the rotor and stator so it was very robust and inexpensive, but it was an essentially fixed speed machine. Variable speed operation was necessary for many applications, machinery, mine winding etc. Variable speed was possible by making an electrical connection to the rotor via brushes and slip-rings - but this goes against the essential simplicity of the machine.
An alternative solution was patented in 1903 in which the slip ring connection was replaced via a second magnetic coupling - the machine having two independent non-interacting fields with a special rotor coupling both fields.
This machine, which became known as the self cascaded machine, gained a reputation for robustness and reliability.
However, the advent of modern power electronics which can generate a variable frequency supply for standard induction machines made both the self-cascaded machine and the slip ring machine obsolete.
At the end of the 19th century there were concerns about energy supplies coal was running out. A combination of more efficient power stations and the discovery of new supplies alleviated this problem.
More recently these concerns have arisen again, plus the concern about climate change. In the 1980s there was the so-called California wind rush. From this chaos the modern wind power industry emerged.
As part of this, the need for variable speed generation became apparent - keeping the tip-speed ratio of a turbine sensibly constant is essential for effective extraction of energy form the wind . The slip ring induction machine was brought out of retirement and is used in most variable speed wind turbines.
However, it is used in a new way. The supply to the rotor is generated electronically and there is a known relationship between mains frequency, rotor frequency and shaft speed. The main advantage is that only a relatively small part of the power need go through the relatively expensive power electronics - this has kept 'fully converted' solutions, in which all the power passes through power elctronics, at bay.
Nevertheless, the brushgear and slip-rings represent both a cost - and more importantly - a reliability issue, as highlighted in studies by my collaborators at Durham University.
It is probably fair to credit Alan Wallace of Oregon State University with the realization that that a self-cascaded machine could be an attractive generator for wind turbines.
The machine, rechristened the brushless doubly fed machine (BDFM), can be used in the same way as the slip ring machine - fixed speed relationship, partial power conversion - but no brushes!
Oregon did not succeed. Shortly before his death, Alan told me in a Manchester curry house that they were building a large prototype but had made some major design errors and that project had run out of funds.
One of Alan's students came to Cambridge to study under Steve Williamson, then Professor of Electrical Power. They built a BDFM and I recall sitting in Steve's office having the theory explained to me.
I thought this machine was really interesting and following Steve's departure started a project on it, with Jan Maciejowski and Tim Flack.
At about the same time I met Peter Tavner, at the time the Technical Director of FKI - Fisher Karpark Industries - which owned Laurence, Scott in Norwich, Brush in Loughborough and DeWind in Luebeck - therefore FKI had a strong interest in this machine.
Once we realized that the matrix algebra and the electrical circuits were saying the same thing we gained a good understanding - possibly the best anywhere - of the machine and 3 MPhils and 3 Phds later here we are, and more underway. The BDFM has also spread to Durham and there have been several final year projects there.
Ehsan Abdi, the second PhD student to work on the machine should be credited with the enthusiasm for starting the commercialization of the machine.
Ehsan was successful in raising funds for Wind Technologies, beginning with our own Challenge Fund and then EEDA, Renewables East, Carbon Connections and the Carbon Trust.
The Wind Turbine
The turbine we see before us was funded by EEDA. The basic turbine is from Gazelle in Newcastle - having a reputation as a well engineered machine in its class.
We re-engineered the drive train with a new gearbox - discovering that mechanical kW are not electrical kW - and a BDFM of our design. We are grateful for the help and assistance of Gazelle.
We used the frame of a commercial induction motor but the rotor - the tricky part - was designed here.
We are deeply indebted to Professor Tavner of Durham and his workshop team, and their sub-contractors, for the construction of the rotor - which was not easy. However, it all came together and worked which was very encouraging.
In addition to the hardware, we devised controllers for maximum power point tracking and the management of reactive power.
It is interesting operating your own wind turbine. You see the fluctuations in output, the effects of gusting. It forces you to think about the performance of the whole system - all parts need to work and reliably - we are not quite ready to submit this machine to Durham's failure mode analysis!
The project shows quite conclusively that it is possible to design and operate a BDFIG.
The turbine is a research tool - we have two PhDs working on the BDFM and have plans to collaborate with the control group.
The turbine also links in with undergraduate teaching as well as research - the recently introduced 4B19 module on wind and wave power has been very popular with students. We have had one 4th year project on the turbine and there should be more in the future.
Many people have contributed to the success of this project. Firstly EEDA for supporting the project.
The technical team - the home team (students, technicians) and Durham University and the staff of Gazelle.
The project would have been impossible without the support and encouragement of the Whittle Lab who have sacrificed some of their BBQ area. We thank the University Estate Management for their help and assistance especially during installation itself.
We thank the Department of Engineering for its support.
Finally, and perhaps most importantly, Lorna Everett for organizing the event today.
Where next?
The present turbine is rated at 20 kW. We have designed a machine for 200 kW which is about to be built at ATB Laurence, Scott with funding from the Carbon Trust.
The stage after that is a 2 MW machine for installation in a wind turbine.