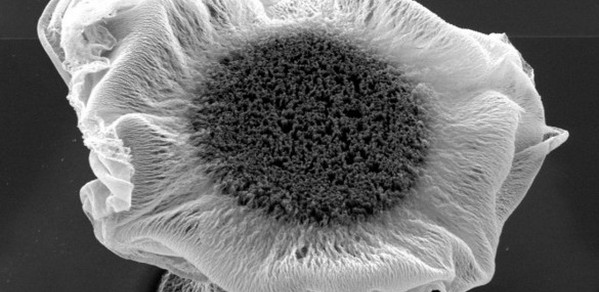
Head of NanoManufacturing at the Department of Engineering’s Institute for Manufacturing (IfM) Dr Michaël de Volder explains why manufacturing carbon nanotubes is so difficult – and so important.
There are still major challenges to overcome before carbon nanotubes can really start to fulfil their potential.
Michaël de Volder
We all know that graphene is the new wonder material – a sheet of carbon just one atom thick which is unbelievably strong, amazingly lightweight, virtually transparent and brilliant at conducting electricity and heat. It has the potential to revolutionise the way we store our energy, clean our drinking water and create a whole new generation of flexible electronic devices. Nanotechnology, in short, is the future. And all this will come from particles which are a hundred thousand times smaller than the width of a human hair.
While much of the hype has tended to be around ‘two-dimensional’ graphene, carbon nanotubes (CNTs) – rolled up sheets of graphene – have been quietly stealing a march. In fact, CNTs have been with us a lot longer than graphene. We know that hollow carbon nanofibres were observed as far back as the 1950s and researchers have been actively researching CNTs since the early 1990s. As a result, the manufacturing techniques for CNTs are comparatively mature, with several thousand tons being produced each year – unlike high quality graphene which is still very difficult to manufacture in large quantities.
But this is by no means the end of the story. While this advance in production capacity is impressive, there are still major challenges to overcome before carbon nanotubes can really start to fulfil their potential. Most engineering applications need materials which are made up of multiple carbon nanotubes – and therein lies the difficulty. While an individual nanoparticle displays all those extraordinary properties, put one next to lots of others without carefully engineering the interactions between them and they start to lose their special powers. In fact, the mechanical and electrical figures of merit of a collection of nanoparticles drop off by at least an order of magnitude when compared to a single particle.
PhD student Sarah Jessl investigating CNT properties with a thermographic analysis tool.
We understand how to make carbon nanotubes and can do so in relatively large quantities. What we now need to learn is how to structure and organise them in such a way that they retain their properties when assembled into a device. And this, to a large extent, is a manufacturing challenge. At the moment, most carbon nanotube products are processed using traditional manufacturing techniques, such as injection moulding of CNT-polymer composites which do not give us any structural control over how the nanoparticles are arranged – and limit the material properties they can deliver. By developing new technologies which allow us to make devices containing well-organised nanoparticles we should be able to achieve a dramatic improvement in their performance and open up a whole raft of new application possibilities.
Which is exactly what the IfM’s NanoManufacturing Group is trying to do. The team was founded just two years ago and is itself a demonstration of rapid scale up, with five engineers, four chemists, two physicists and two material scientists already in post. The nanomanufacturing challenge is such a complex one that we need a multidisciplinary team to address it, as well as the collaboration of other universities, a broad spectrum of industries, and closer to home, collaborators in the Departments of Engineering, Materials Science, Chemistry, Chemical Engineering, and the Cavendish Laboratory. We also work very closely with other research centres at the IfM which are similarly engaged in developing new advanced materials and manufacturing processes.
A good example of this collaborative approach is the EPSRC-funded project, ‘Advanced Nanotube Application and Manufacturing Initiative’, which is bringing together engineers and materials scientists from the Universities of Cambridge and Ulster with a group of industrial partners to scale up a unique method for fabricating sheets and yarns of aligned carbon nanotubes. These will be used in next-generation lightweight composites, and can provide a much lighter alternative to copper wires in, for example, aerospace applications and high performance electric motors.
A variety of 3D CNT microstructures fabricated by a process developed by IfM’s NanoManufacturing group in collaboration with the Mechanosynthesis Group at MIT.
The IfM’s NanoManufacturing Group is also focusing on the development of technologies which can organise nanoparticles into hierarchical superstructures. To achieve this, we are researching how to simultaneously optimise material properties at three length scales: at the nanoscale on surface chemistry, at the microscale on form and structure and at the large scale to integrate the particles into devices. With funding from the European Research Council, the European Union’s Marie Curie scheme and the EPSRC, the Group is exploring new ways of fabricating such carbon nanotube-based devices by, for instance, combining lithography with chemical engineering techniques.
We have already made a significant breakthrough in the manufacturing of microstructured surfaces, which was published in a recent issue of Nature Communications. Microstructured surfaces can exhibit a variety of useful properties, including controllable mechanical stiffness and strength. They can even replicate the intricate structures found on the skins of certain plants and animals, making it possible to produce surfaces which have, say, the water-repellent or adhesive characteristics displayed by some insects. This particular technique works by causing carbon nanotubes to bend as they grow and form controllable complex shapes in three dimensions (see right). The process could also be used to engineer other properties, such as electrical and thermal conductivity and chemical reactivity, by attaching various coatings to the carbon nanotubes. In the meantime, our technique is already being put to good use, making surfaces which are being used as chemical microsensors, batteries and biomimetic smart surfaces.
From left to right: Shahab Ahmad, Hadi Modarres, George Chandramohan, Jean de la Verpilliere, Jae-Hee Han (Visiting Professor), Michaël De Volder, David Beesley, Nicolo Chiodarelli, Davor Copic, Sarah Jessl, Laura Maggini.
The promise of nanotechnology is such that billions of dollars of public money have been and continue to be spent on research by national governments. We are now reaching a tipping point where we understand the physical properties of many nanoparticles and how to produce them sufficiently well to start them on their journey to commercialisation. Indeed, it may come as a surprise to learn that CNTs are already being used commercially in a variety of products ranging from sporting goods and batteries to cars and bullet proof vests. This is only the beginning: we will soon see these small but mighty structures being put to many different uses.
This article originally appeared in IfM Review.